Are you doing everything you can to maintain the efficiency of your storage space?
This article covers nineteen simple tips that you may be able to implement across the whole stock and order management lifecycle.
I will cover:
PS - If you would like to fast forward to the part where we tell you about how we can help, why not read our Warehouse Efficiency or Order Management pages?
Procurement
During the procurement process, several proactive steps can be taken to contribute to a more efficient warehouse.
1. Choose suppliers carefully
Choose suppliers who have a track record of reliability and timeliness in delivery. Reliable suppliers ensure that your warehouse receives the necessary inventory on time, reducing delays and potential disruptions in operations.
2. Negotiate favourable terms
Negotiate favourable terms with suppliers, including pricing, payment terms, delivery schedules, and minimum order quantities. Cost-effective procurement can help reduce overall operational costs, making resources available for investing in warehouse efficiency improvements.
3. Commit to inventory management techniques
Adopting specific inventory management techniques will help you become more strategic in your procurement.
By employing various methodologies such as just-in-time (JIT), ABC analysis, FIFO (First-In, First-Out), and LIFO (Last-In, First-Out), you can navigate overstocking or understocking issues.
The more that these processes can become standardised within your business, the more streamlined your procurement will be.
It will reduce the need for multiple approvals, and ensures consistency in inventory quality, which means smoother warehouse operations downstream.
Pre-receiving
"Pre-receiving" refers to preparing for the receipt of incoming shipments before they physically arrive at the warehouse.
This process involves various activities aimed at ensuring that the warehouse is ready to process incoming inventory.
4. Enhance your communication
Establish clear communication channels between your suppliers, procurement, receiving, and other relevant departments to share critical information such as expected delivery times, quantities, and special handling instructions.
This effective communication helps coordinate resources and ensure timely preparation for incoming shipments.
5. Digitise and automate your documentation
By replacing manual paperwork with digital systems, errors are reduced, and data becomes more accurate and accessible. Automated processes mean quicker information sharing, enabling better coordination between departments.
Real-time updates on the status of incoming shipments allows for proactive decision-making and pre-allocation of human resources. For example, our eCommerce platform can directly receive advanced shipping notifications (ASNs) when integrated with your suppliers.
Additionally, digital documentation simplifies auditing and compliance procedures, saving time and increasing the opportunity for insight and learning.
Receiving
Improving receiving efficiency is critical for warehouse operations as it directly impacts inventory management, order fulfilment, and customer satisfaction.
Below are several steps that can be taken to enhance receiving efficiency, but you may wish to read our article ‘How to improve your receiving efficiency and accuracy’ for a deep dive into the topic.
6. Visually inspect and document the inventory
Conduct a visual inspection of the incoming inventory to assess its condition and contents, and document your findings in a pre-receiving report. This report should include any discrepancies or issues that were identified.
The checks should include cross-referencing the received items with the information provided in the Bill of Lading (BOL) or ASN.
By promptly identifying discrepancies or issues, such as damaged goods or incorrect shipments, warehouse staff can take corrective action before items are put into storage. This minimises disruptions to downstream operations, reduces the risk of stockouts or delays, and maintains inventory integrity.
Additionally, documenting findings provides valuable data for improving supplier relationships, optimising inventory management processes, and promoting continuous improvement efforts in the warehouse.
7. Consider how you intend to use your space
At this point, you should begin to consider the space you have available to you.
Considerations include:
- Where will vehicles unload inventory? Will this conflict with courier arrivals for shipment collection?
- Has space been logically allocated for unloading inventory, away from packing and dispatch areas?
- Is there sufficient space for the typical quantity of inventory you receive?
Ensure your receiving area marks the beginning of a circular flow, minimising congestion and streamlining inventory movement from receiving to storage and dispatch.
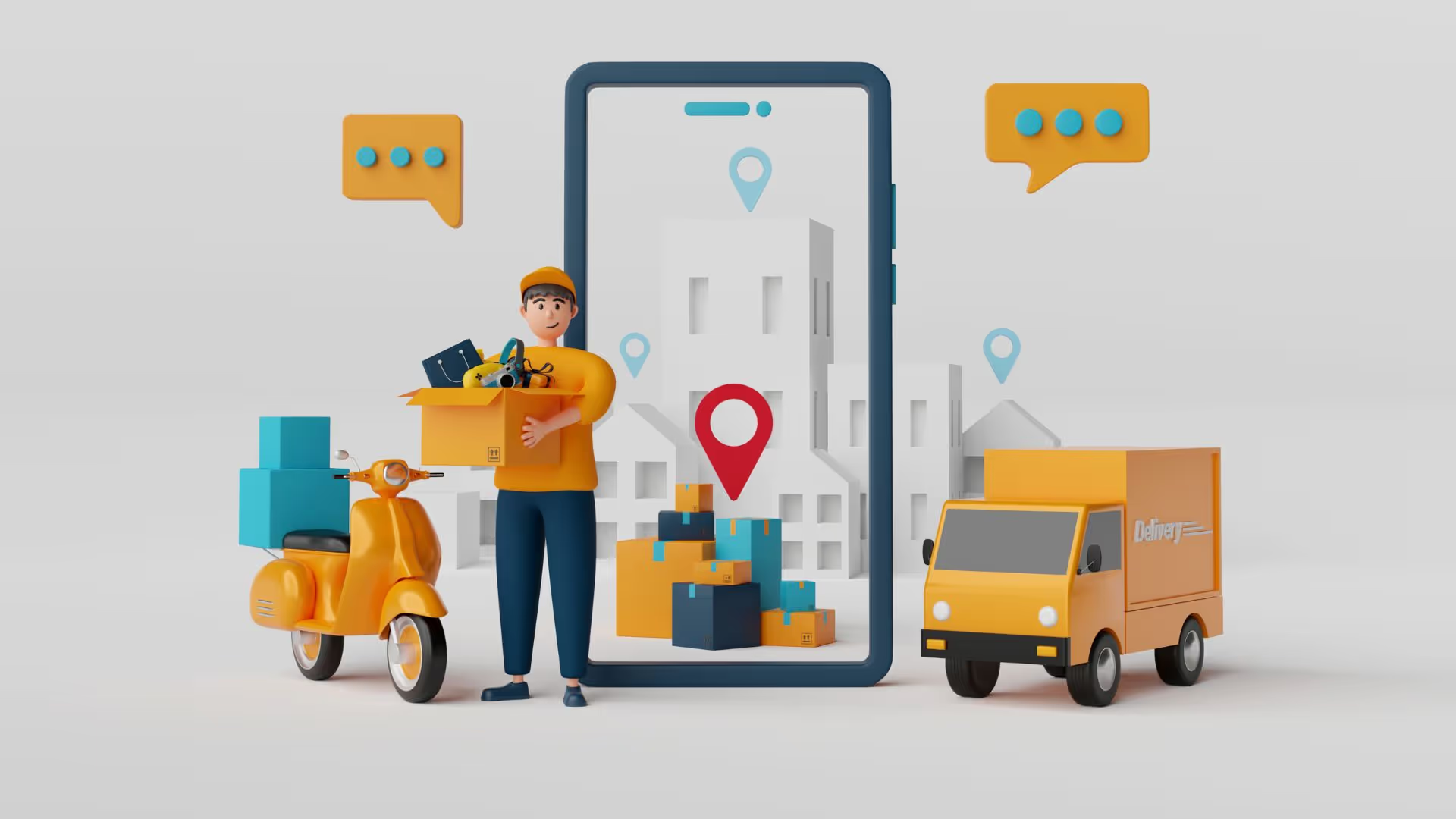
Putaway
Now that we have received the new inventory, the focus turns to managing the movement of goods through the warehouse.
This begins with storing the inventory, a process commonly known as 'putaway'.
8. Define Standard Operating Procedures (SOPs)
Establish standardised procedures for the putaway process, including guidelines for prioritisation, slotting, and storage allocation.
Location assignment
Based on predetermined criteria such as SKU, product type, or demand, warehouse personnel can be directed to assign storage locations for the new inventory. This ensures efficient retrieval during picking operations.
Storage allocation
The inventory is placed in designated storage locations according to the location assignment. Designate storage locations based on product characteristics, storage requirements, and picking frequency.
Organise storage racks, shelves, and bins logically to facilitate easy access and efficient movement of goods during putaway and retrieval, and take advantage of as much vertical spacing as possible to maximise your available space.
A good practice is to aim for 88% utilisation, depending on the volume of stock, to allow for some growth.
Inventory documentation
Warehouse personnel must update your inventory management system with details of the newly received inventory, including SKU, quantity, location, and any relevant information.
Our receiving software automatically logs new inventory into the system, allowing warehouse personnel to scan and document inventory directly from the pallet.
Safety and compliance
Warehouse personnel adhere to safety protocols and compliance regulations while handling and storing the new inventory. This includes proper stacking, labelling, and handling procedures to prevent accidents and ensure regulatory compliance.
9. Labelling and indexing
Effectively labelling and indexing racks, shelves, and bins helps to streamline inventory putaway and picking by providing clearly identifying storage locations. This reduces search time, minimises errors, and enhances organisation, ensuring faster and more accurate retrieval of items during both inbound putaway and outbound picking.
We often recommend using inserts for labelling, as they provide flexibility for renaming allocated storage over time. However, once racks are organised and labeled, there is rarely a need to rename them.
Picking
Efficiency in order picking is crucial, as it directly influences your capacity to serve customers.
10. Optimise your warehouse layout
Design your warehouse layout to minimise travel time between picking locations. Organise your inventory strategically, placing frequently picked items closer to packing and shipping areas to reduce travel distances.
11. Implement picking strategies
Different picking strategies offers different benefits and can be tailored to suit the specific needs, requirements and layout of a warehouse.
Batch Picking
Multiple orders are picked simultaneously by a single picker. This strategy reduces travel time and increases productivity by consolidating similar items or orders into a single picking run.
Zone Picking
Dividing the warehouse into zones, with each picker responsible for picking orders within their designated zone. This strategy promotes specialisation and minimises travel time by assigning specific areas to individual pickers.
Cluster Picking
Combining elements of batch picking and zone picking by assigning clusters of orders to each picker within their designated zone. Pickers then pick multiple orders simultaneously within their cluster.
Wave Picking
Orders are grouped into waves based on criteria such as order priority, destination, or product type. Pickers then fulfil orders within each wave sequentially, allowing for better coordination.
Discrete Picking
Picking one order at a time, typically suited for low-volume or high-value items. While it may not be as efficient as batch picking for high-volume orders, discrete picking ensures accuracy and precision.
Piece Picking
Individual items are picked from their storage locations to fulfil specific orders. It is commonly used for eCommerce or retail orders where each item may be unique or require special handling.
Pick and Pass
Orders are passed through multiple pickers stationed along the picking route. Each picker is responsible for picking specific items or sections of the order before passing it along to the next picker, reducing congestion through a continuous flow of orders.
Batch and Sort
Picking items in batches and then sorting them into individual orders at a separate sorting area. This strategy allows for efficient picking of similar items while maintaining order accuracy during the sorting process.
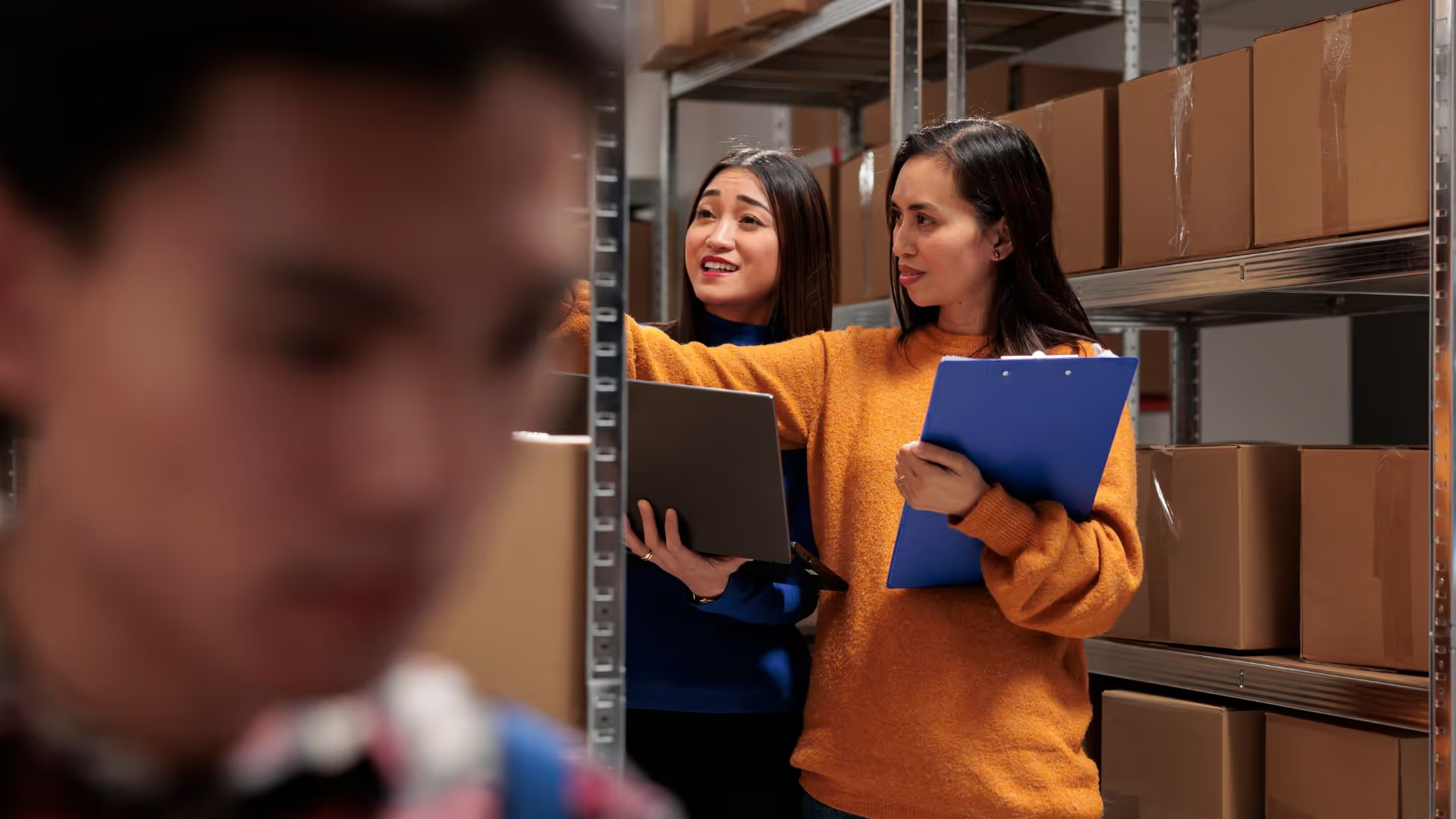
12. Pick path optimisation
Pick path optimisation utilises algorithms to determine the most efficient route for pickers to navigate through the warehouse.
By analysing factors such as item location, order priority, and picker location, these apps can guide pickers along the optimal path, minimising their travel time and maximising their productivity.
This is covered within our order management technology under our directed picking feature.
13. Pick verification
Pick verification features enable real-time confirmation of picked items. Pickers use handheld technology to scan each item as they pick it, verifying that it matches the item listed on the order.
Packing
Ensuring that your orders are packed accurately and in good time.
14. Establish a packing station
By consolidating packing activities in one designated area, you can minimise unnecessary movement and congestion, leading to faster order processing. A well-equipped packing station allows for efficient organisation of packaging materials, tools, and equipment, optimising workflow and reducing packing time.
Additionally, having a designated packing area improves quality control and order accuracy, as packers can focus on each order without distractions, ultimately ensuring that orders are packed correctly and ready for shipment promptly.
15. Pack verification
Checking items against the order before packing them minimises the risk of missing or incorrect items. It’s a proactive approach to maintain order accuracy.
Additionally, pack verification measures contribute to overall efficiency by reducing the need for rework and order rectification, allowing orders to be processed smoothly and expediently.
This is covered within our order management technology under our Pack Check feature.
16. Standardise your packing procedures
Much like the putaway process, you can establish standardised packing procedures outlining routine steps for preparing and packaging orders.
You can keep consistent and minimise errors by clearly documenting packing instructions, such as the correct materials to use, and labelling requirements.
Develop packing checklists or packing slips that list the items to be packed in each order. Use barcodes or QR codes to scan and verify items against the packing list, and keep packaging material close to the packing bays for easy access.
17. Run quality control checks
Incorporate quality control checks into the packing process to verify the accuracy and condition of packed orders. Inspect packages for damage, missing items, or incorrect labelling before sealing and shipping to prevent returns.
Dispatch
Finally, we come to the dispatch process. At this stage, your work should be all but done, but there are still one or two efficiency boosters to be considered.
18. Choose a logical pick-up location
You can make loading easier by strategically choosing a location that minimises travel time and congestion and is as close to vehicle access as possible. This helps carriers to turn their collections around quickly.
It also reduces the distance and effort required for loading operations. As well as speeding up the loading process, this also minimises manual handling and labour costs.
19. Prioritise orders for dispatch
Establish prioritisation criteria for order dispatch based on factors such as order urgency, customer preferences, and delivery deadlines. Prioritise high-priority orders or time-sensitive shipments to ensure they are dispatched promptly and delivered on time.
Final thoughts - Build a culture of continuous improvement
As you come to the end of the inventory and order management life cycle, you should take regular opportunities to review and evaluate each of the components from procurement right through to dispatch.
Identify opportunities for improvement and optimisation. Solicit feedback from staff, monitor key performance indicators (KPIs), and implement corrective actions to drive continuous improvement efforts.
Find out more about how our technology can help you drastically improve the efficiency of your warehouse.
Our recent posts
Keep up to date with the latest news and insight from the team at Venditan
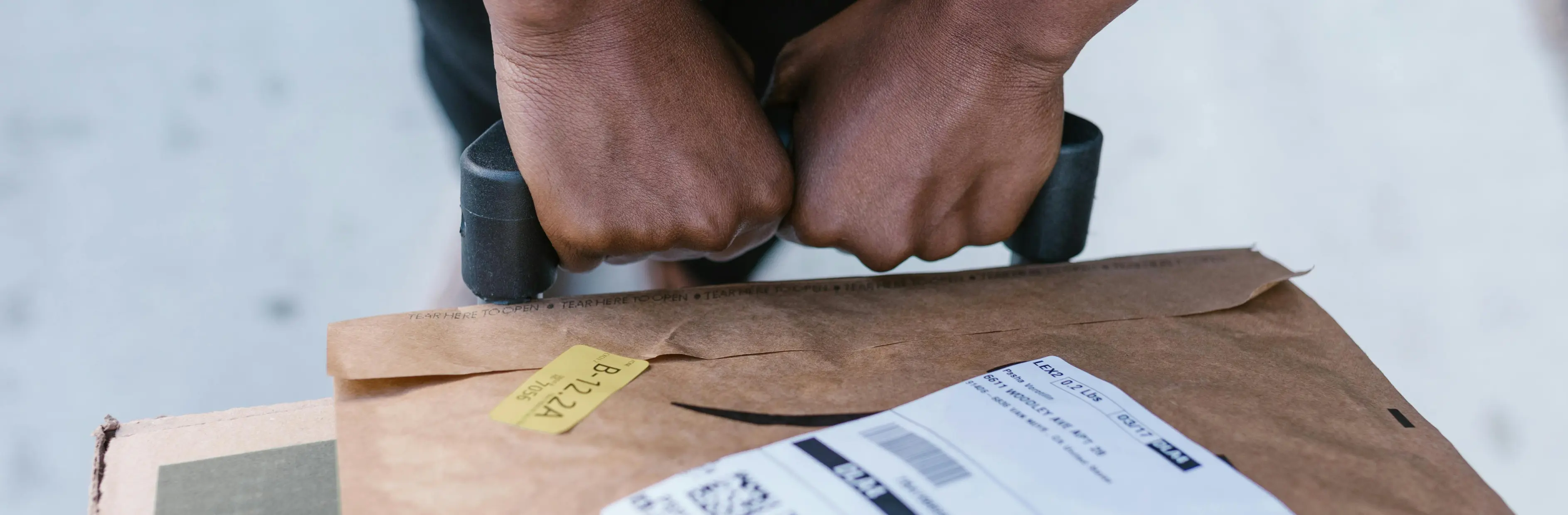
.webp)
-p-2000.webp)
.webp)
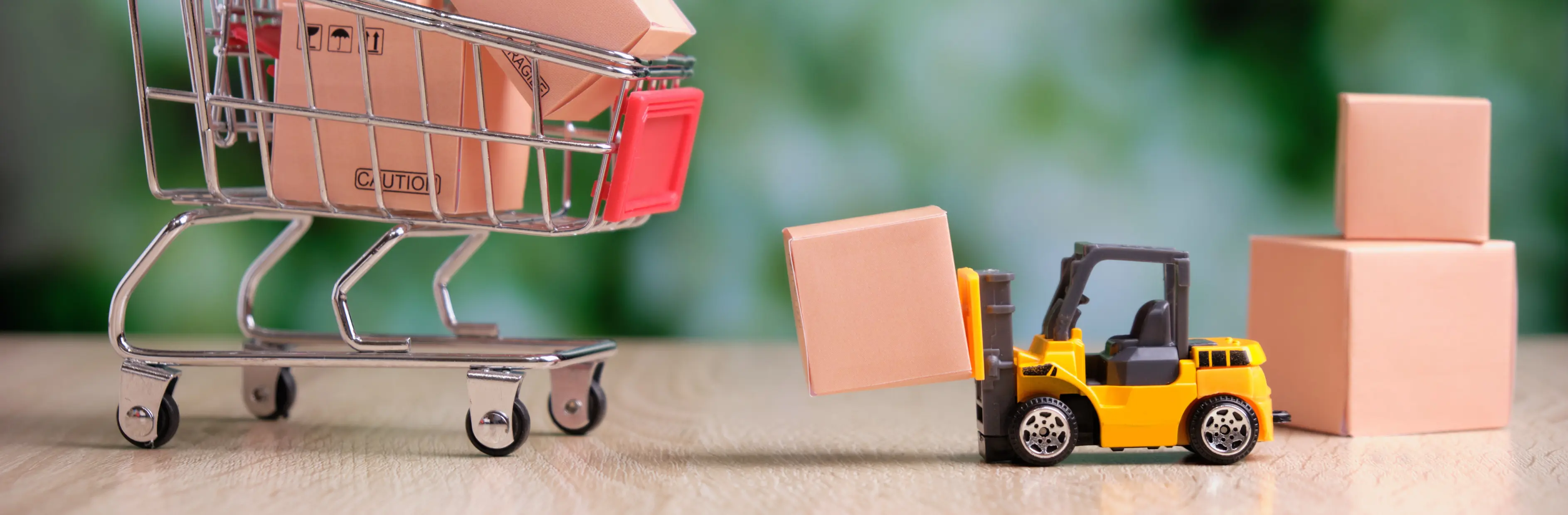